AIRBUS site de Rochefort
Les objectifs et attentes du client
Le groupe AIRBUS a fixé des objectifs énergétiques ambitieux à l’horizon 2030 :
- Réduction des consommations en énergie primaire de -20% vis-à-vis de 2015, soit un objectif de réduction de 4 700 GWh/an sur la globalité du site.
- Réduction des émissions de CO2 de -85% vis-à-vis de 2015, soit un objectif de réduction de 2 500 tonnes CO2/an sur la globalité du site.
AIRBUS a mandaté BEST ENERGIES en 2023 pour la réalisation d’une première étude de faisabilité technico-économique concernant la décarbonation globale du site AIRBUS de Méaulte.
Suite à cette étude, AIRBUS a confié une mission complémentaire à BEST ENERGIES en 2024 afin d’étudier la récupération d’énergie fatale sur les cabines de peinture grâce à la mise en place de systèmes de récupération de chaleur fatale.
Nos principales missions
Le projet de décarbonation du site vise à réduire au maximum les consommations en énergie fossile tout en proposant un projet rentable financièrement.
Le process de fabrication du site de Méaulte intègre des phases de peinture des pièces d’avion. Pour ce faire, des cabines de peinture consomment du gaz pour leur process. Le réchauffage d’air est ainsi effectué par un brûleur gaz présent directement dans les gaines de soufflage de chaque cabine.
L’objectif de la mission est de réduire ces consommations d’énergie primaire en récupérant un maximum de chaleur fatale sur l’air extrait des cabines. Ces calories permettront de préchauffer l’air neuf.
Airbus souhaitait étudier uniquement les roues thermiques de récupération. Nous avons suggéré d’étudier d’autres systèmes tels que les échangeurs à plaques air/air ainsi que les batteries à eau glycolée.
Nous avons également étudié des scénarios avec le réseau de chaleur EnR proposé lors de la première mission (géothermie, biomasse, gaz).
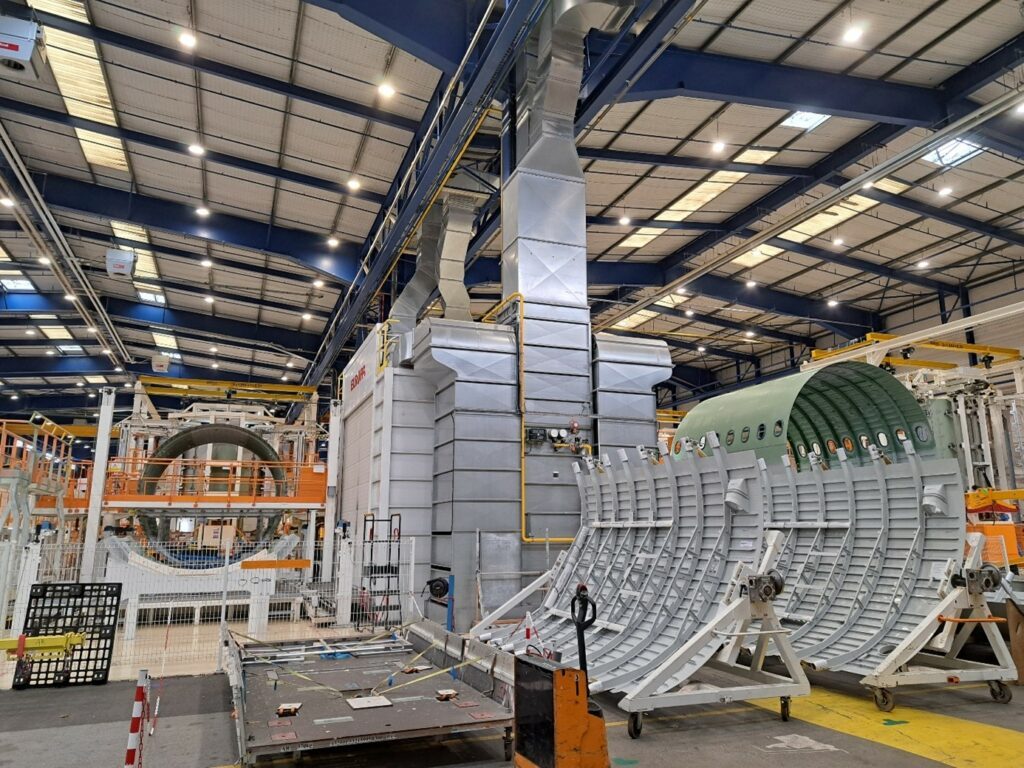
Caractéristiques du projet
Sur un créneau de travail de 8h, les cabines ont des cycles de réchauffage d’air de 2 x 2 h à 45°C et un maintien à 23°C le reste du temps.
Les cabines de peinture sont situées dans les bâtiments CH1, CH2, CH3, CH4, J de l’usine.
Le périmètre des cabines retenues pour l’étude concerne un total de 6 cabines :
- Bâtiment CH1 : 1 cabine OMIA
- Bâtiment CH2 : 1 cabine OMIA
- Bâtiment CH3 : 2 cabines, OMIA et EUROPA
- Bâtiment CH4 : 1 cabine OMIA en construction
- Bâtiment J : 1 cabine SECOMAT
Des sous-compteurs gaz sont présents sur les cabines et ont permis d’obtenir les valeurs index gaz en m3.
Les puissances appelées horaires et besoins utiles ont été calculés par cabine suivant leur fonctionnement, les index gaz, les débits de soufflage et les températures extérieures.
Les puissances appelées par les cabines vont de 100 kW à 600 kW.
Les débits d’air varient de 50 000 à 95 000 m3/h suivant la cabine et les gaines d’air.
Ces valeur sont utilisées dans la suite de l’étude pour le dimensionnement des outils de récupération de chaleur.
Résultats obtenus
Les scénarios proposés dans l’étude sont les suivants :
S0 : Situation actuelle,
S1 : Roue thermique de récupération,
S2 : Echangeur air/air,
S3 : Batteries eau glycolée en gaine,
S4 : Situation actuelle + Réseau de chaleur (S0),
S5 : Situation actuelle + Batteries eau + Réseau de chaleur (S3+S4).
Les caractéristiques des systèmes de récupération ont été appliqués suivant les scénarios à chaque cabine de peinture.
Cette mission m’a permis de découvrir le secteur de l’aéronautique et ses contraintes techniques. Notamment les informations et données inexistantes rendant l’étude des besoins très délicate. Les échanges avec les équipes Airbus ont été très importants. L’interlocuteur principal a été réactif et investi dans la recherche d’informations nécessaires à la mission. Ce projet m’a permis d’étudier la récupération de chaleur fatale sur des cabines de peinture industrielles. J’ai pu établir une synthèse technique des systèmes de récupération sur un large scope de débits et de puissances.
Léa, Cheffe de projet Best Energies